How can you reduce the risk of supply chain disruptions? What are some robust strategies? What are the best practices, and if not followed how does that affect costs?
In a perfect world, business operations run according to plan and cargo always arrives at its destination on time, but anyone involved in supply chain management knows that this couldn’t be farther from reality. One delay can mean a dozen tons of rotten avocados or a spoiled pallet of pharmaceuticals. A security disruption could cost you a shipment of electronics and stick you with the bill.
The good news is that many losses through disruption are preventable but require careful planning. So, how does one begin such a daunting process? Below, we will break down a list of risks that modern logistics stakeholders should have on their radar and introduce how industry leaders use probability theory and optimization to form their risk management strategies.
Heists and the Digital age
In January of this year, the Transported Asset Protection Association (TAPA) reported an 18.5 percent increase in year-over-year losses across the EMEA region. Thefts included apparel, electronics, tobacco, food and beverage products.
As the push toward digitalization continues, we are seeing more and more airports and forwarders embrace paperless practices. However, with more sensitive data being shared via software platforms, it’s not just your shipment, it’s your data that’s catching the eyes of opportunistic pirates of the digital age.
There’s no one-size-fits-all solution for theft and data security, but it’s worth talking with your forwarders, carriers, shipping and technology partners about their security protocols, which security validations they have, and what their approach to data privacy is.
Terrorism
While less common than other sources of disruption, terrorist activity is another reality that needs to be taken into account when assessing risk, especially in dealing with air freight. 2016 was a tumultuous year in the EMEA region, with three major incidents of significance. Istanbul experienced two attacks, just weeks apart in the spring of that year. And just months before that, the bombing at Brussels Airport knocked out cargo operations for some time.
Both Istanbul and Brussels airports recovered rather quickly, the flow of passengers and cargo resuming after only a few days, but operations were nevertheless delayed. Forwarding companies were forced to reroute flights, causing a ripple through the supply chain.
Both airports featured sophisticated security systems, proving that terrorism can rear its ugly head anywhere. When considering this risk, shippers and forwarders need to make sure that their lines of communication are open, so that customers know where their shipments are and can plan for delays and reroutes.
Brexit
Brexit is a national phenomenon with global implications. With the implications of Brexit looming, stakeholders should be prepared for shifts in business-as-usual as the potential effects of tariffs on E.U.-U.K. trade transition into a tangible reality.
Recently, another development was made in the Brexit timeline, the U.K. government announcing a 20-month “transitional period” that will end in December 2020. This will allow U.K. and E.U. companies linked through the supply chain a grace period to grapple with the looming effects of new tariffs on company-to-company dynamics. The U.K.’s secession also means the evaporation of long-existing open skies agreements and cross-border policies, still yet to be renegotiated.
So, while the transitional period is good news for concerned parties, the time should be utilized to prepare for the worst; there is potential that come the end of 2020, no progress will have been made in government relations. Unless the E.U. and U.K. can agree, industry experts predict that controls and regulations will be implemented, resulting inevitably in heavy congestion at ports that will limit capacity.
Even if Brexit isn’t on your radar, there are protectionist developments underway on almost every continent. Advice on supply chain management during a trade war could fill a stack of books, but until you have time to read them, keep an eye towards flexibility, vendors with multinational footprints, and logistics partners that have extensive alliances in the regions you operate.
Weather
Weather is another factor out of our hands, and unfortunately, the occurrences of extreme weather conditions like hurricanes are increasing. The number of category four and five hurricanes has more than doubled since the 1970s, and it looks like we’re in for another powerful hurricane season.
But it’s not just tropical storms that pose a risk to logistics. A report from the Environment Agency suggests that one sixth of property in the U.K. is at risk of flooding. The U.K. business community endured a slow recovery of Storm Desmond in 2015 which caused a domino effect through the supply chain and disabled some 200 businesses’ operations.
Every major natural disaster brings its share of disruption. Warehouses are knocked out, airports shut down, and roads are unusable. Make sure you work with companies that can shift resources and personnel during extreme conditions, and who can move quickly when necessary.
Man-made delays
Apart from the above mentioned incidental delays, one can reduce the risk of supply chain disruptions by setting and following proper and relevant operating procedures.
Documentary delays are perfect examples of man-made delays which could result in huge cost implications to the customer(s) by way of demurrage, detention, port storage, etc. These delays may be caused due to the customer not following the set operating procedures or the operating procedures that are set not being sufficient.
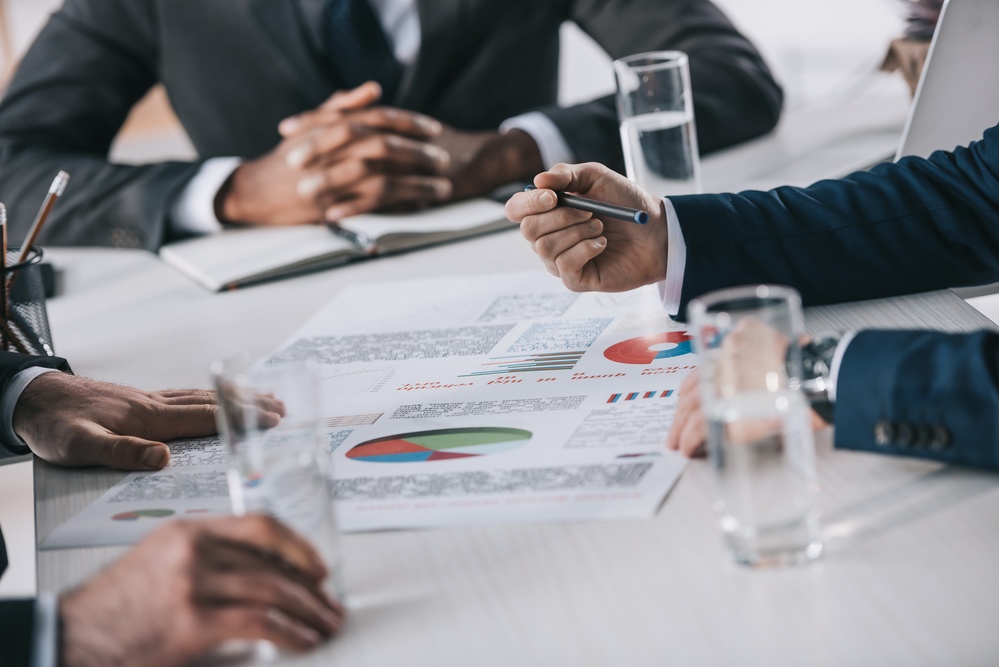
Adopt Best Practices
Adopting best practices in the process of trade is of great importance to reduce the risk of supply chain disruptions.
- Improving the turn around of inventory is an absolute must for effective supply chain operations
- Being lean and mean in supply chain management is important to ensure that inventory is under control and there is no excess
- Measuring and monitoring supplier performance to ensure efficient deliveries
- Optimizing the supply chain cycle from order creation till delivery
- Putting your eggs in different baskets as in creating a few supply chain networks within your organization to achieve unit/product based profitability
- Using measurement metrics that satisfy the business and not the management
- Go digital and use the best supply chain technology available in the market currently to ensure competitiveness
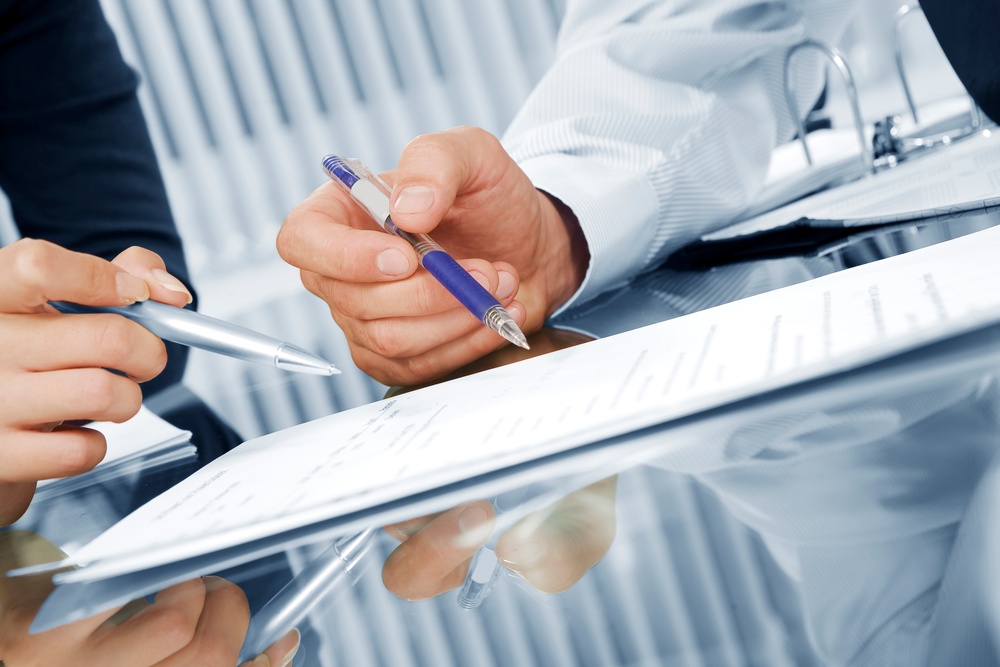
Risks are not of the Same Magnitude- What now?
In evaluating your company’s risks, it is important to consider that all risks are not of the same magnitude -- more to the point, risks have varying mathematical probabilities, and each one has a different associated cost. The imposition of a new tariff is going to have a different cost associated with it than a heist or a hurricane would, and each one of them has a different probability of occurring.
These two components -- probability and potential cost -- determine the monetary threat of a risk to your business. To state the obvious, there should certainly be a plan in place for a risk with a high probability of occurring and a great potential cost to the company. Perhaps the potential cost of a severe weather incident versus the resulting cost of a terrorist incident on freight transportation is about the same, but one is much more likely to occur than the other.
Exploring an instance of the more likely scenario, let’s remember the production disruption Honda dealt with back in 2014 when a delayed delivery of parts due to adverse weather conditions caused its operations in Swindon, United Kingdom to come to a screeching halt -- yet Honda was able to give its customers a guarantee that this incident would not push back the delivery of shipments. How was it able to assure this? It had a previously agreed upon policy's with its workforce that allowed them to redistribute the lost hours into a condensed amount of time upon the arrival of the late shipment. We will call this Strategy A.
One might consider an alternative strategy to prepare for a scenario, which we can call Strategy B. Why not order parts in advance and warehouse the inventory until the start of production? You would never have to worry about a late shipment suspending production again. Operations managers can tell you why this is not a viable solution in two simple words: inventory costs.
If it costs the company $50,000 in facilities per year to ensure that there is always enough supply on hand, but a potential supply chain disruption that may never occur at all would only cost the company $20,000, what is the point in taking the measures in the first place?
So, it becomes an optimization equation -- the objective being to minimize cost subject to some important outside factors: the probability the risk will occur, and the cost associated with that risk. If Honda’s project managers determined severe weather conditions to be a risk that is sure to occur fairly regularly, they would have likely deemed it wise to invest in more padding around production deadline and opted for Strategy B, instead. In reality, this problem is rare enough that it is not financially prudent to invest so much into inventory storage.
It’s safe to assume that while the weather incident probably cost Honda a pretty penny in labor costs, it is a much less expensive mitigation strategy than pouring money into inventory facilities each month.
Not only is Strategy A a less expensive solution, but it is also more versatile, meaning it’s applicable to various other scenarios in which a kink in the supply chain causes a stall in production -- be it severe weather conditions, a security breach, a terrorist attack -- the strategy still fits. In these other scenarios, an overstocked warehouse containing 100 extra units of part x isn’t a solution, but a workforce that is able to remain flexible in the face of an array of different scenarios is. Here, Honda was able to identify a solution that addresses various risks, which should be every risk manager’s goal.
Supply chain disruptions shouldn’t be treated as unlikely scenarios, but eventual certainties. The key is to stay ahead of the curve by knowing the potential costs associated with worst-case scenarios and to have protocol already in place when these eventualities occur. Many companies are already implementing in-depth plans in preparation for the forthcoming effects of Brexit, NAFTA renegotiations, possible trade wars, and arranging secondary sources of capacity and supply before the inevitable scramble that will occur in the face of increased demand.
The list of potential supply chain disruptions could go on forever, but the key insight to take away is not to obsess or panic, but to invest time and money in analyzing your company’s specific risks and to try to consider the big picture moving forward.